While drawing tube to change its dimensions is nothing new, drawing with a tightly controlled dynamic mandrel is a unique technology that can impart a varying wall thickness.
Editor’s note: This article covers a specific tube drawing process. For an overview of drawing, see “Tube Drawing Principles.” Bendable Copper Tubing
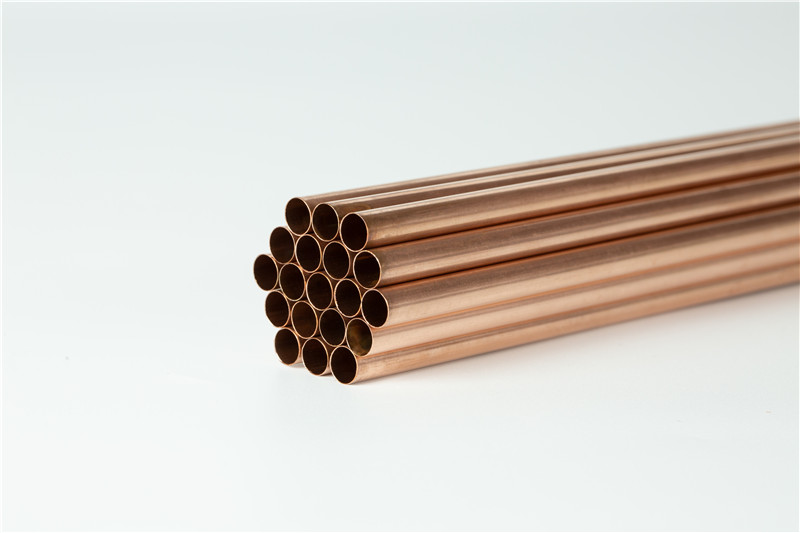
Drawing a tube on a draw bench is nothing new. Whether the bench uses a carriage pulled by a chain or uses a hydraulic system to operate the draw carriage, the process can change the tube’s OD, ID, and wall thickness. Drawing also can improve the surface finish and even refine the grain structure.
The simplest drawing process, sinking, reduces the OD and ID and may change the wall thickness, depending on the die’s design and the tube’s D/t ratio. An equipment operator uses a pointing process to reduce the tube’s OD at one end, then feeds the pointed end through the die. From there, the draw bench does the rest, pulling the entire length of tube through the die.
“Drawn tubing has been around for a hundred years,” said Paul Russo, president and co-owner of George A. Mitchell Co. “Drawing with a floating mandrel, semifloating or full floating, has been around for many years too.” Other common drawing processes use fixed mandrels. The mandrel, sometimes called a mandrel plug, is inserted inside the pointed tube, is advanced until it approaches the die bearing, and seats in a stationary position at the start of the draw.
While these processes are more than adequate for many drawing applications, engineers at George A. Mitchell Co. saw a way to devise a variation on the conventional drawing process. This innovative process involves moving the mandrel to vary the ID as the tube is being pulled.
Although many products are made from material of a constant wall thickness, whether it’s plate, sheet, pipe, tube, or profile, many products also would benefit from having a varying wall thickness. Using the lightest-gauge material for much of a product and heavier material only where it’s needed—for strength, for welding to another workpiece, for threading, or for some other design characteristic—would optimize material consumption and product weight.
To vary a tube’s ID, the engineers at Mitchell came up with a mandrel on a mandrel rod programmed for dynamic motion. The die has an included angle and a straight bearing, while the mandrel has a critically designed taper. The mandrel motion is controlled with precision during the drawing process, and the result is a tube tailor-made for its application—a tube with a varying wall thickness.
“Moving a mandrel is nothing new,” Russo said. “Controlling a mandrel’s static position—for example to compensate for wear—has been done for a long time via mandrel screw adjustment devices.”
Although this technology has potential in countless applications, the staff at Mitchell has found the most use in the automotive industry.
While drawing tube to change its dimensions is nothing new, drawing with a tightly controlled dynamic mandrel is a unique technology that can impart a varying wall thickness.
“Many sports cars have aluminum tubular drive shafts,” Russo said. “Taking out the weight along the tube’s length helps to cut the vehicle’s weight, and this technology can thicken it at the ends where it needs strength to attach to the transmission and the differential,” he said.
Using a thin-walled aluminum tube for a drive shaft might sound like a recipe for disaster, especially given the torque typically developed by a high-performance automobile, but it’s not.
“The stiffness comes from the diameter much more than the wall thickness,” Russo said. “The stiffness calculation takes the diameter to the fourth power.”
At least one automotive crush tip design uses a drawn tube that has a varying wall thickness. The crush tip, also known as a crash box, is located between the bumper and chassis to absorb some of the energy of an impact so that less of that energy is transferred to the passenger cabin. It’s like a shock absorber that works only once.
Because the crush tip gets compressed in stages, with the thinnest section crumpling first, it provides a graduated, progressive resistance to the impact. As the thicker sections compress, they absorb progressively greater amounts of energy. Although impacts happen suddenly, this sort of crush tip compresses relatively gradually.
The thought behind the design of this crush tip is somewhat sophisticated, but this technology makes the solution both simple and elegant. And it arguably provides better impact protection than a crush tip with homogenous characteristics.
Bicycle designs also benefit greatly from this variety of specially made, variable-wall tubes. “Some composite bicycle frames are weighed in ounces,” Russo said. “Steel frames aren’t that light, but this technology helps.” Many high-performance mountain bikes are made from AISI 4130, also known as chrome-moly, which is ideal for racing and other applications that need strength without weight. It’s an aircraft-quality, medium-carbon, low-alloy steel that has some chromium and molybdenum for strength. Beefing it up at the ends allows joining to other tubes by welding.
Applications for this technology go well beyond manufacturing to the search for precious ores, gems, petroleum, and natural gas. “These tubes are thin-walled along their length and have heavier walls at the ends for ID and OD threading,” Russo said.
“Some of the pipes made by this method had to go to an exploratory [drilling] site which, by its nature, is remote,” Russo said. It was so remote, in fact, that some of the materials, like the drill tubes, were brought in by helicopter.
“Making these tubes as light as possible makes the transportation step more efficient,” Russo said. It takes no small amount of fuel every hour to keep a helicopter aloft, and loading it down with cargo makes it much more expensive still. Lighter tubes mean more per trip.
While drawing tube to change its dimensions is nothing new, drawing with a tightly controlled dynamic mandrel is a unique technology that can impart a varying wall thickness.
Variable-wall tubes can be long—the longest Russo knows of is 33 ft.—and part designers have nearly all of the freedom they have with conventional drawing processes. The dynamic mandrel drawing system can impart round or oval IDs, with just one caveat: The ID must be symmetrical on both the X and Y axes. Beyond these parameters, the potential for other applications is boundless.
“Imagination is the limit,” Russo said.
See More by Eric Lundin
Eric Lundin worked on The Tube & Pipe Journal from 2000 to 2022.
Read more from this issue
Subscribe to The Tube & Pipe Journal
The Tube & Pipe Journal became the first magazine dedicated to serving the metal tube and pipe industry in 1990. Today, it remains the only North American publication devoted to this industry, and it has become the most trusted source of information for tube and pipe professionals.
Easily access valuable industry resources now with full access to the digital edition of The Fabricator.
Easily access valuable industry resources now with full access to the digital edition of The Welder.
Easily access valuable industry resources now with full access to the digital edition of The Tube & Pipe Journal.
Easily access valuable industry resources now with full access to the digital edition of The Fabricator en Español.
In this episode of The Fabricator Podcast, and in partnership with Miller Electric, Andy Weyenberg from Miller's motorsports...
© 2023 FMA Communications, Inc. All rights reserved.

Refrigeration Tube Dehydrated Not yet registered? Sign up