Poor service practices can lead to contaminants entering a refrigeration system, resulting in premature failure. When installing and repairing refrigeration equipment, technicians should always follow good service practices to prevent any contaminants from entering the piping or system components.
The most common system contaminant is atmospheric air; however, there are other potential contaminants that could also enter a system such as copper shavings, flux, copper oxide, dirt, and sandpaper particles. Atmospheric air contains oxygen, nitrogen, and water vapor. If oxygen and water vapor remain in a system, they could react with the compressor oil and the heat generated in the system and produce acids. Nitrogen left in the system will collect in the condenser and cause the system’s high-pressure side to operate at elevated pressures. 1x1 Aluminum Square Tubing
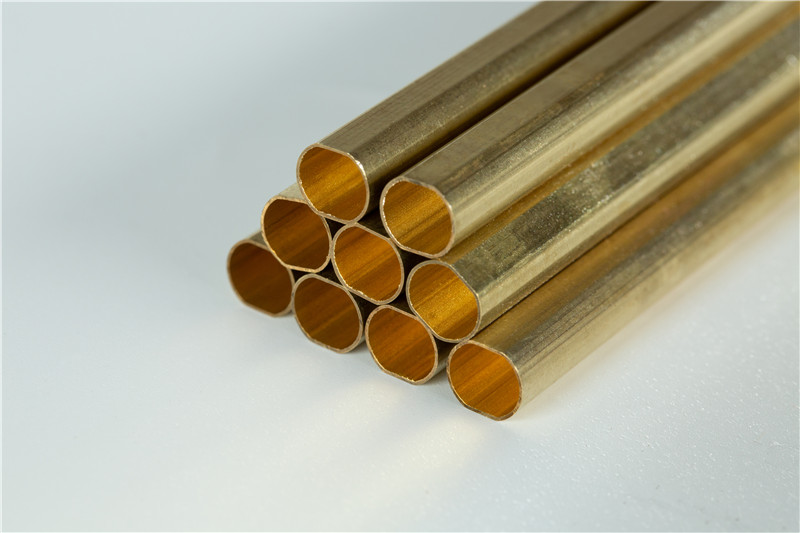
Atmospheric air will enter a system any time it is opened for repair or during its initial installation. Following proper evacuation techniques will remove this contaminant. Use a quality vacuum gauge and pump and follow the manufacturer’s recommendations for the required micron level to be achieved. Many manufacturers will recommend the system’s pressure be reduced to a vacuum level of 500 microns or below. Avoid taking shortcuts during this process.
When adding refrigerant to a system, atmospheric air can also enter through the refrigerant hoses and manifold. Remember to always purge the hoses and manifold before adding refrigerant.
Copper shavings, flux, copper oxide, dirt, and sandpaper particles that have entered the system could cause a refrigerant restriction or damage to a compressor. Again, always follow proper installation and repair procedures to avoid these contaminants from entering a system. For example, new ACR tubing comes with its ends sealed to prevent any contaminant from entering the tubing during transportation and storage. When installing this tubing, leave the tube ends sealed until it needs to be connected.
Any unused tubing that may be used later needs to be resealed. If possible, reuse the caps that were on the tubing originally. For years I have used electrical tape. To prevent the glue from the tape getting on the tube end while taping, I simply start wrapping the tube end with the non-glue side in contact with the tubing. Then after a few wraps, twist the tape and now wrap with the glued end in contact with the tape and not the tubing. This will eliminate any glue from the tape coming into contact with the tubing, which will make cleaning the tube end a lot simpler when it comes time to use it.
While preparing the tube ends for brazing, always be cautious of how you deburr and clean the ends. While cutting and deburring, position the tube end so no copper shavings enter it. Avoid using sandpaper to clean the tube end; a Scotchbrite pad is generally a better choice. If you do need to use sandpaper, position the end to avoid any of the grit from entering the tubing and wipe the tube ends with a clean, soft cloth to get rid of any grit.
To prevent copper oxidation while brazing, sweep a non-oxidizing gas such as nitrogen through the tubing. A nitrogen sweep of 1 to 2 cfm through the tubing is an effective means of expelling any oxygen from the inside of the tubing, which will prevent the formation of oxidation on the inner walls. If oxidation develops inside the tubing, it can flake off and be carried throughout the system along with the refrigerant and oil.
And, of course, always change out the filter-drier any time the system is opened for a repair, and make sure one is installed on the system during the initial installation. A properly installed filter-drier will absorb any water vapor remaining in the system and filter out any particulates. However, do not rely on a filter-drier as a catch-all for sloppy repair or installation procedures. A filter-drier should be viewed as an additional precaution to guard against contaminants circulating throughout a system and not a replacement for following good service practices.
Joe Marchese is an author, instructor and HVACR service contractor. He can be reached at joe@koldcraft.com.
You must have JavaScript enabled to enjoy a limited number of articles over the next 30 days.
Sponsored Content is a special paid section where industry companies provide high quality, objective, non-commercial content around topics of interest to the ACHR News audience. All Sponsored Content is supplied by the advertising company. Interested in participating in our Sponsored Content section? Contact your local rep.
On Demand Don’t miss your chance to learn from industry thought leaders and gain valuable insight on how the A2L transition will affect your HVAC business!
This webinar will focus on the many benefits of R-32 refrigerant as the best refrigerant to meet the EPA requirements for GWP below 700, beginning January 1, 2025.
Copyright ©2023. All Rights Reserved BNP Media.

Aluminium Brass Tube Design, CMS, Hosting & Web Development :: ePublishing