As the MENA region develops more aerospace manufacturing facilities, Julien Fabreguette, chief executive at Epi - part of the platforms and systems cluster at the UAE’s defence conglomerate Edge - explains what it takes for a precision machining company to become an aerospace shop.
Julien Fabreguette, chief executive at Epi (Image: Edge Group) Anodized Cnc Machining Parts

Aerospace manufacturing must be precise. Lives, infrastructure and critical assets depend on the reliability and dependability of aircraft parts produced within aerospace shops. When governments and organisations need precision machined parts, such as vertical fin ribs, wing components, shroud sets or otherwise, they will often seek out highly capable precision machining companies for these highly complex parts. A precision machining company is an ideal place for aerospace machining and parts engineering, but in order to become successful, safe and reliable, these shops must include comprehensive certifications, equipment and capabilities.
In essence, aerospace manufacturing produces parts for aircraft, missiles, and spacecraft. The best aerospace production plants are expansive and highly-automated, inclusive of expert staff engineers, operating a high calibre of CNC machines as well as other high-tech industrial kit. While certain aerospace fabrication or general machining shops employ some of the same techniques and equipment as other manufacturing operations, manufacturing aerospace parts requires best industry quality standards and considerably more administrative foresight.
To become a legitimate participant in the industry, organisations must complete several different certifications and registrations that attest to stringent quality management at every level of the manufacturing process, ensuring their components meet the engineering standards and strict tolerances required.
The most important certifications an aerospace machine shop must have are the ISO 9100:2018 and the EN/AS 9100. Completing accreditations with organisations such as Nadcap are also invaluable to obtain within the defence and aerospace industries. The ISO certifies that systems, processes, and documentation procedures meet the standard for quality and consistency and is the international management standard for the aircraft, space, and defence industry, ensuring the safety of aircraft occupants. The EN/AS 9100 standard expands on that standard but has more specific requirements for aerospace manufacturers.
Any successful aerospace manufacturing shop must include the latest advancements in machining technology and equipment. CNC machines, multitasking equipment, and automation, such as a multi palleted machines and modular tooling, are all part of a technologically advanced machine shop. High-quality equipment, professional automated surface treatment processes and even live tooling are key fabrication aspects for an aerospace shop.
Every standard machine shop includes basic milling and turning centres, yet creating an aerospace shop that consistently delivers export quality components demand tools and manufacturing ability that exceed the baseline requirements. Machining large five axis prismatic aerostructure components from both aluminium and titanium demand a high calibre of machine to fulfil the intricate details and tight profile and positional tolerances. The speed capabilities and power of the spindles are essential when equipping the aerospace shop.
Frequently investing in advanced equipment is essential when offering the standard of aerospace precision machining. But beyond possessing impressive equipment, the best aerospace machine shops will also provide advanced tooling paired with quality assurance systems.
Time is consistently a factor during manufacturing. For that reason, in-house tooling for aerospace machining is essential; for many aerospace components, one challenging process is developing tooling that efficiently accommodates complex geometry parts. Developing custom tools and fixtures in-house translates toward drastic time-savings within both inspection and production, creating a more successful shop.
Precision engineers must ensure that quality and accuracy go into every piece machined. On some major assembly lines, if one machined piece is incorrect, the entire operation will stop. This is why the finest CNC machining centres and the most advanced quality assurance equipment will accomplish nothing without an expert team of engineers. When building aerospace machining company, it must include a team backed by solid education, continual training and extensive experience. An ideal shop is one that hires engineers and machinists that understand the relationship between design constraints and machining.
The aerospace industry demands the highest level of precision. An effective aerospace shop must ensure quality with the best certifications, invest in the latest equipment, and leverage in-house expertise results in consistent, repeatable processes. The net effect of the certifications, registrations, and high-quality equipment combined with excellent internal operations result in cost-effective, reliable solutions. Top-quality machining, tooling, quality control and testing standards certify the complex delivery on which the aerospace industry depends.
With extensive expertise of more than 25 years in the field of aerospace manufacturing, Fabreguette’s experience is critical to the platforms & systems cluster. At Edge Group
Prior to his current role, he was senior vice president of operations at Strata manufacturing, and a board director of Strata Solvay Advance Material.
He had previously been managing director of Airbus Helicopters in Mexico, where he was responsible for organising and executing the creation of a new aero structures manufacturing plant for Airbus Group.
Subscribe to the free Times Aerospace newsletter and receive the latest content every week. We'll never share your email address.
Rolls-Royce has announced Turkish Airlines will order 100 Trent XWB-84 engines and 40 Rolls-Royce Trent XWB-97 engines.
Aviation, defence and space news from the Middle East, Africa and South Asia
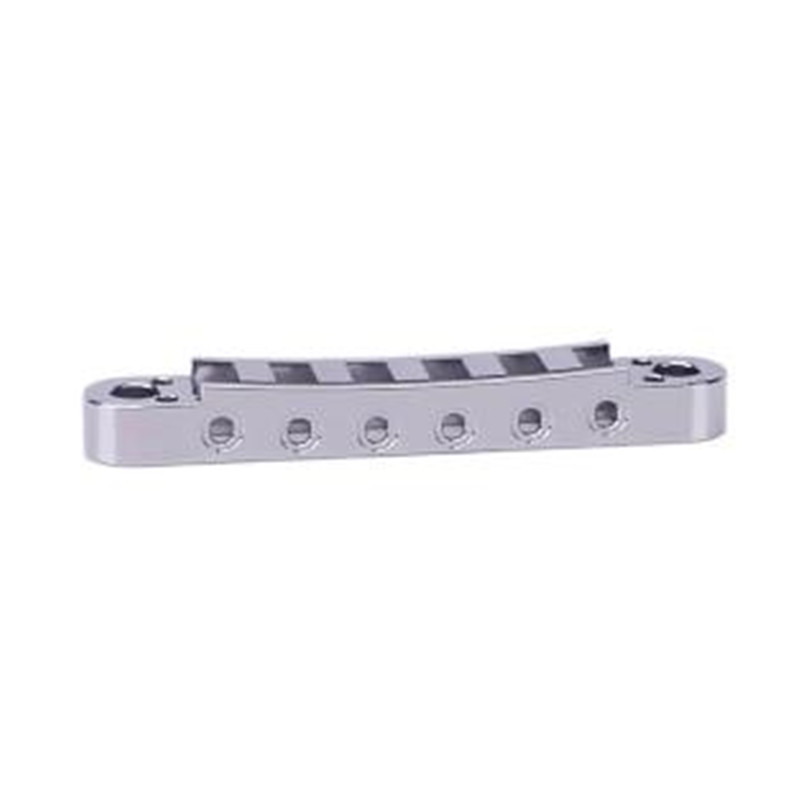
Cnc 5 Axis Aluminum Turning Parts Copyright © 2021 Times Aerospace Publishing Ltd, a Tarsus Group company. All rights reserved. Privacy policy.