For some years now, wood has received an increasing amount of attention in the construction industry. With concerns raised about sustainability and the carbon footprint of buildings, new construction methods and innovative possibilities in the use of timber have developed rapidly. This interest in wood stems in part from its renewability, though this benefit is contingent on sustainable logging and the appropriate management of forests to be allowed to regenerate naturally. However, it is the versatility of wood that serves as the primary impetus for its widespread use. From boards, to beams, to floors, and even to thermal and acoustic tiles and insulators, wood can be used in several different stages of a single project and with different degrees of processing and finishing.
In the case of the manufacture of furniture, wall coverings, ceilings, and even floors, the use of boards is an economical and functional way of incorporating wood into buildings. There are several options for wooden boards on the market, and each uses a different manufacturing process involving fibers, particles, fragments, or sheets, resulting in specific uses. Next, we select the most commonly used wooden boards, including their characteristics and main uses: Birch Veneer Tape
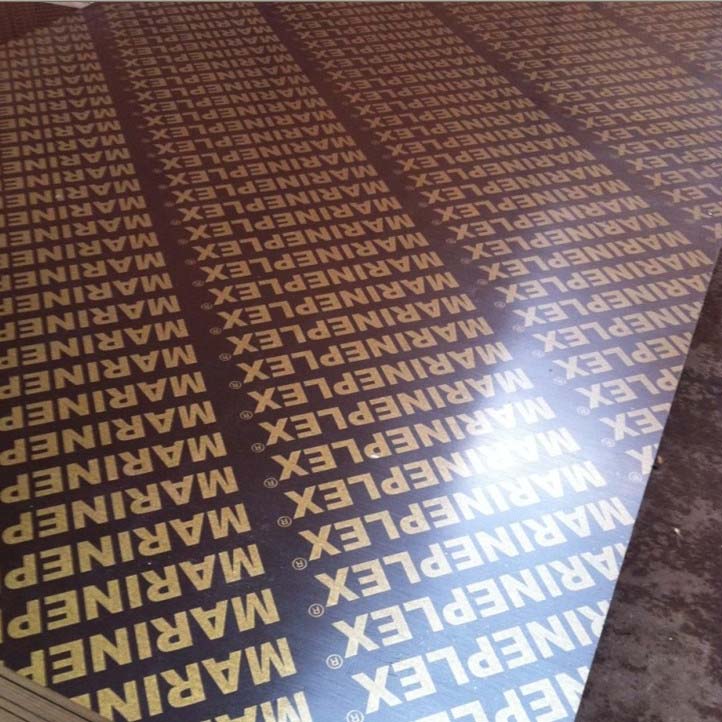
MDF boards are made of wood fibers bonded by synthetic resin and compressed through pressure and heat, resulting in a solid and very uniform board with good finish and durability. Because the fibers are randomly oriented, the machine can cut them in any direction, delivering a smooth surface to the touch. Naturally, the board does not resist water well, but there do exist options on the market that are more resistant to moisture and sometimes even fire.
Currently, MDF boards are the most used material for carpentry, as they are compatible with a number of different finishes including simple and lacquered paint, glued from natural sheets or melamines, or even pattern printing. But they can also be used elsewhere, such as in wall and door claddings.
The HDF (High Density Fiberboard) is very similar to the MDF, though their manufacturing processes differ. Being compressed under higher pressure, these boards are more resistant, support more weight, and can cover larger extensions.
Chipboard and MDP (Medium Density Particleboard)
Chipboard is created by pressing wood debris, such as sawdust and dust, with resin and glue. Over time, this material has given way to other solutions such as the MDF or its nearest replacement, the MDP. It can be finished with paints and varnishes, but they rarely stick, since the surface is not smooth or uniform. The main advantage of this agglomerate is its low cost. Its uses are similar to MDF, but specific types of hardware and connections must be used to obtain a satisfactory result.
Like Chipboard, MDP boards are also made of wood particles compressed with synthetic resin and heat pressed, with the difference that the fine particles are deposited on the face of the board and the thickest particles in the core. This distribution allows a better finish, a better adjustability, and more possibilities of application for claddings. It is not very resistant to moisture and may have some imperfections.
The resulting panels are widely used in the production of simple furniture.
Plywood boards are made of overlapping wood sheets glued perpendicularly and heat pressed. Just as with cross laminated timber (CLT), cross-directional fibers in plywood allow the board to withstand greater stress.
Plywood's use is quite varied. It can be used for furniture, floors, ceilings, doors, and countertops among others. It is also compatible with paints and glues of natural sheets or melamine.
OSB boards have a very characteristic aesthetic that has been increasingly incorporated into architectural design. These boards are made of wood chips pressed in perpendicular layers and bonded with resin applied at high pressure and temperature. They have good mechanical strength and rigidity. In addition to their good sound insulation, they have no empty spaces inside them, and no knots or cracks, so they are very uniform. They are also ecological and durable against the outdoors and the action of rain, humidity, wind, and heat. In addition, the boards are fully recyclable. However, since they have a rough surface, it is impossible to apply laminated products onto them.
The main applications of OSB occur in walls and ceilings, floor bases for the application of carpets, wood floors, bricks, cladding and construction sheds, packaging, and furniture structure among others.
Editor's Note: This article was originally published on October 10, 2019, and updated on October 9, 2020.
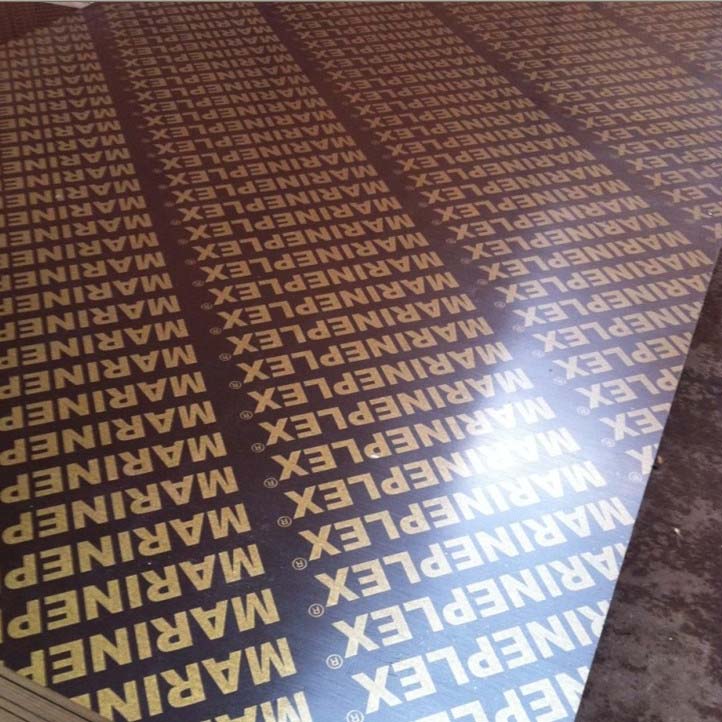
Marble Like Wood Veneer You'll now receive updates based on what you follow! Personalize your stream and start following your favorite authors, offices and users.